Ever looked at a half-finished building site and wondered, "What are they actually using to build all this?" It’s not as mysterious as it looks. The stuff that goes into construction is surprisingly basic—just five big names top the list. These aren’t just boring materials lying around. They’re what literally shape our cities, homes, and pretty much any structure that lasts more than a week.
If you’re thinking about a project—maybe a deck out back or something bigger—the type of raw material you pick makes a huge difference. Go for the wrong option, and you’ll be worrying about cracks, rust, or rot way too soon. The right material means fewer headaches and way less maintenance. So, knowing what’s at the foundation of construction isn’t just for engineers; it helps anyone who’s doing a build or just wants to avoid picking the wrong stuff for a renovation. Ready to break down what these main raw materials actually do?
- Stone and Aggregates: The Groundwork
- Cement: The Binding Force
- Steel: The Backbone
- Timber: Nature’s Gift
- Bricks: Old School, Still Cool
- Choosing the Right Material: Quick Tips and Insights
Stone and Aggregates: The Groundwork
Think of stone and aggregates as the muscle under your house or road. Crushed stone, gravel, and sand aren’t there for looks—they make sure everything sits rock solid. Aggregates make up about 60% to 80% of most concrete mixes, which means for every bag of cement you see, there’s a much bigger pile of crushed rock and sand behind it. That’s a huge piece of any construction budget.
Why are they always used? Apart from being everywhere and fairly cheap, they’re tough. Aggregates help concrete handle weight, stop cracks from spreading, and stick around for decades with barely any fuss. Without them, concrete would just crumble.
- Raw materials like limestone, basalt, or granite make the best aggregates because they’re durable and weather-resistant.
- Sand fills the gaps between bigger rocks, making mixes more tightly packed and stable.
- Even roads, driveways, and train tracks depend on different-sized aggregates. Smaller stones go under pavers for a flat surface, bigger chunks form the base layers of highways.
Here’s a tip if you’re building something yourself: always check where your aggregate comes from. Good suppliers will happily tell you the source and make sure it’s clean. Dirty or low-quality aggregates can mess up your concrete mix, leading to weak spots and headaches later.
So, next time you walk on a sidewalk or drive over a new street, remember you’re literally moving over layers of carefully selected rock. It’s the stuff that keeps everything steady.
Cement: The Binding Force
Cement is basically the glue of modern construction. Without it, you wouldn’t have concrete, mortar, or anything that holds bricks and stones together for long. When people talk about cement, they’re usually thinking of Portland cement, which is the one used in almost every building you see today.
Here’s the key fact: cement isn’t used on its own. It gets mixed with sand, aggregates, and water to form concrete or with sand and water for mortar. This mixture is what gives sidewalks, bridges, and skyscrapers their staying power.
The secret sauce in cement is its ability to react with water—a process called hydration. As cement hydrates, it gets rock hard and holds everything together. No other material comes close when you need something to set like stone in just a few hours.
- About 4.4 billion tons of cement were produced worldwide in 2023.
- Cement production is energy-intensive; it accounts for up to 8% of global carbon dioxide emissions.
- There are different types like Ordinary Portland Cement, Rapid Hardening Cement, and White Cement—the choice depends on what you’re building and how fast you need it to set.
If you want strong, crack-free concrete, get your mixing ratio right. Most projects use a 1:2:4 ratio: one part cement, two parts sand, four parts aggregates. Always add water little by little until it feels like oatmeal—not soupy, but not dry either.
Check out this quick table breaking down the basics of cement use:
Type | Common Use | Setting Time |
---|---|---|
Ordinary Portland Cement | General construction | Initial: 30 min / Final: 10 hrs |
Rapid Hardening | Road repair, precast work | Initial: 30 min / Final: 8 hrs |
White Cement | Decorative works | Initial: 30 min / Final: 10 hrs |
If there’s one raw material you can’t ignore on a site, it’s cement. Skip it or skimp on it, and you’ll feel it when the project crumbles ahead of schedule.
Steel: The Backbone
If there’s a single raw material you’ll see everywhere on a construction site, it’s steel. This stuff is the unsung hero holding up everything from houses to stadiums. Walk through any modern city and you’ll notice—nearly all the tallest buildings depend on steel frames to keep them standing strong and safe. No wonder it’s called "the backbone" of construction.
So, why is steel so popular? For starters, it’s insanely strong for its weight. Engineers love it because you can build big, open spaces without a maze of walls and columns getting in the way. Steel is super flexible, too, which helps buildings survive earthquakes and high winds without collapsing. Plus, it goes up fast—modular steel parts can be bolted together on-site way quicker than pouring concrete for every single floor.
Here’s something wild: Nearly steel used in construction comes from recycled scrap. That makes it one of the most sustainable building materials around, cutting down on wasted resources and energy use compared to making new steel from scratch. Want numbers? Around 98% of all steel used in construction is recycled at the end of a building’s life. That’s just good sense—both for the wallet and the planet.
Steel isn’t all the same, though. There are a few main types you’ll run into:
- Structural steel: Beams, columns, and framing parts in big buildings.
- Reinforcement (rebar): Bars that strengthen concrete.
- Sheet steel: Roofing, wall panels, and sometimes even flooring.
Here’s a quick table with useful stats about steel in construction:
Property | Value/Fact |
---|---|
Typical strength (yield) | 250–550 MPa |
Recyclability | 98% reused |
Average lifespan in a building | 50–100 years or more |
Main uses | Framing, reinforcement, roofing |
If you’re picking materials, consider this tip: Use galvanized or stainless steel in spots where moisture is a problem—think basements, outdoor frames, or kitchens—since untreated steel can rust. It costs more upfront, but you’ll save a ton on repairs and repainting down the line.
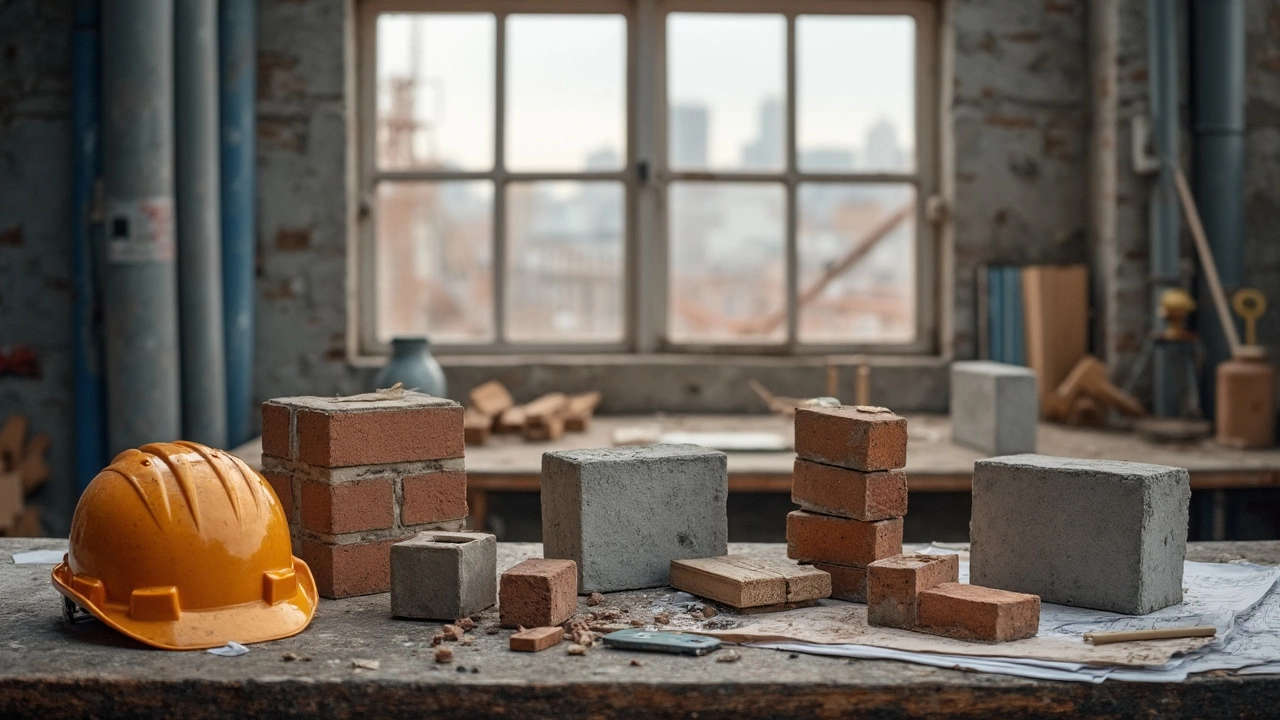
Timber: Nature’s Gift
Timber is the go-to material whenever you want something sustainable, easy to work with, and surprisingly strong. It’s not just for old cabins and farmhouses—think modern homes, framing for buildings, even tall structures called "mass timber skyscrapers." Timber performs way better than most people expect. In fact, cross-laminated timber (CLT) panels can handle loads that rival concrete, but with a fraction of the weight. That’s why architects across the world are using it for greener, cost-effective designs.
There’s more to timber than just planks you grab from the hardware store. Let’s break down the most common types used in construction:
- Softwood: Think pine, spruce, and fir. Grows fast, costs less, and works for framing or roofing.
- Hardwood: Oak, maple, and beech. Heavier, tougher, and often chosen for things that need to last, like flooring or fancy paneling.
- Engineered Timber: Stuff like plywood, CLT, and LVL (laminated veneer lumber). Super versatile and stronger than plain sawn wood.
Timber isn’t just about looks or going old-school. It’s renewable—trees grow back. It’s easy to cut, drill, and nail compared to metals or stone. If you need something that’s quick to put together and offers some natural insulation, timber’s a solid choice.
Serious bonus: Wood buildings trap carbon. A ton of timber stores about 1.6 tons of CO₂. Switch out steel or concrete for CLT, and you slash emissions big time. Check out this quick comparison:
Material | CO₂ Emissions per Ton (kg) | Renewable? |
---|---|---|
Timber | -1,600 (stores CO₂) | Yes |
Steel | 1,800 | No |
Cement | 930 | No |
Timber isn’t perfect—it can rot, burn, and get eaten by termites. To keep it strong, use treated timber for anything outdoors and check building codes for fire rules. If you’re tackling a DIY project or a full house build, always ask your supplier about sustainably harvested wood. Certified wood, like FSC or PEFC, means forests are replanted and treated right.
Bricks: Old School, Still Cool
If you think bricks are boring, think again. These chunky rectangles have been around for more than 7,000 years, and there’s a reason we’re still stacking them today. They handle heat, rain, wind, and fire without breaking a sweat. That’s why you’ll spot brickwork everywhere—from houses in London to ancient walls in Babylon.
Bricks are usually made from clay and fired in huge kilns, which makes them tough and pretty much weatherproof. Some newer versions mix in concrete or fly ash for extra strength or eco-friendliness. The main draw? Bricks last decades with almost no maintenance if laid right, and their strong thermal mass means your house stays warmer in the winter and cooler in the summer.
Check out some quick stats that show why bricks are still a go-to choice:
Property | Details |
---|---|
Compressive Strength | Up to 35 MPa (clay), 50+ MPa (concrete) |
Fire Resistance | 4+ hours (typical wall) |
Lifespan | 100+ years |
Thermal Mass | High—reduces temperature swings |
Bricks aren’t just strong—they look good, age well, and help out with insulation. Fun fact: the Great Wall of China is mostly made from bricks in its later sections, and those have stood for centuries despite all kinds of weather.
Looking to use bricks in your own project? Here are a few tips that make a difference:
- Always check the local climate—bricks handle freeze-thaw cycles better than a lot of other materials.
- Use good mortar. Even the best brick won’t last if the mortar falls apart first.
- Don’t skip on the foundation—bricks are heavy, so a solid base is key.
- Consider recycled bricks for small builds or accent walls. They’re cheaper and have tons of character.
Bricks still hold up against modern options, both when it comes to looks and what they can handle. They’re a sturdy pick for anyone thinking long-term, making them a real contender among construction materials.
Choosing the Right Material: Quick Tips and Insights
Picking the right construction material sounds simple, but it’s where things usually go sideways in a project. If you want your build to last and not drain your wallet later with fixes, it’s all about getting this decision right from the start. Here’s what you want to keep in mind, whether it’s for a new home, fixing up a shed, or going big with a commercial spot.
First, look at what you actually need for your environment. Going for timber? Great, but it rots fast in damp areas without treatment. Steel is super strong, but throw it in a salty coastal town and rust can eat it alive without proper coatings. Cement handles weather like a champ but needs good drainage so it doesn’t crack in the freeze-thaw cycle.
- Budget smart: Aggregates and locally sourced stone are affordable for big projects. If you buy exotic stuff or steel, prices shoot up.
- Think about maintenance: Timber asks for ongoing upkeep; steel needs anti-rust care; bricks can last decades with almost zero fuss.
- Keep an eye on local building codes: Some areas ban certain materials for safety or environmental reasons, like flammable finishes or cheap composite woods.
- Go green if you can: There are recycled steel and eco-friendly concrete mixes. Timber from certified sources can shrink your build’s carbon footprint.
- Factor in the load and lifespan: For anything holding real weight—think floors or beams—steel and reinforced concrete usually win.
For a quick look at how different materials compare, check out this breakdown:
Material | Strength (MPa) | Average Lifespan (years) | Main Weakness |
---|---|---|---|
Stone & Aggregates | 20-100 | 50+ | Heavy, tricky to shape |
Cement | 20-40 (plain) | 50+ | Cracking if not reinforced or if drainage is bad |
Steel | 250-550 | 50-100 | Rusts without coating |
Timber | 40-80 (for hard woods) | 30-50 | Rot and pests |
Bricks | 5-30 | 100+ | Can be slow to lay; cracks under stress |
No material is perfect for every single job. The trick is lining up the pros and cons of each for your climate, the load you’re handling, your budget, and how much maintenance you’re cool with. And here’s something a lot of people miss—sometimes, mixing materials (like using steel for the frame and bricks for the outer skin) gives you the best of both worlds.
Bottom line? Set your goals for the project, ask questions, and don’t just go for what’s trendy. Solid research beats a rushed choice every time, and your structure will thank you for it down the line.