Wood holds a funny place in our minds. It’s classic, warm, and everywhere in daily life. At the same time, if you ever sat around a campfire, you know it’s not the most fireproof stuff. Here’s the kicker: the vast majority of homes you walk past every day are built from the same thing you’d toss in a campfire—wood. Welcome to the world of Type 5 building construction, the workhorse of suburban America, and the go-to for the houses that line nearly every neighborhood.
What Exactly Is Type 5 Building Construction?
Type 5 construction, sometimes just called "wood frame," is all about flexibility and speed. This construction type lets builders use any structurally sound wood (sometimes even engineered wood like Glulam beams or laminated veneer lumber) for load-bearing walls, floors, and roofs. If you’re picturing a classic stick-built house with 2x4 or 2x6 studs, wooden rafters, and plywood sheathing, you’re spot on. This isn’t just for small houses, either—low-rise apartments, townhouses, and even mixed-use commercial spaces can be Type 5, especially when you see that boom in new neighborhoods springing up seemingly overnight.
How did it become so common? Well, it’s as much about the rules as the resources. Building codes shape what types of structures get built. Type 5 is the most relaxed of the standard construction types. It allows wood almost everywhere, while types 1 through 4 require more fire-resistant materials. By law, Type 5 buildings usually max out at three stories (sometimes four, depending on local codes and fire protection measures), mainly because wood has its limits when it comes to supporting weight and resisting fire. If you've ever wondered why apartment buildings often top out at just four floors before switching to concrete, now you know—the code draws a line.
The upside? Type 5 is less expensive and much faster to build than anything using steel or masonry. For developers, that’s a big draw. For buyers, this means more affordable homes and apartments. It’s also adaptable—builders can cut and reshape wood on-site, work around weird lot shapes, and make cozy details that would cost a fortune with concrete or steel. The real pro? Maintenance is usually simple. Need to knock out a wall? Repair a floor? Type 5 makes it doable without heavy tools or special skills.
The downside? Fire risk and weather vulnerability, which we’ll get into next. This tradeoff between speed/ease and safety sets the stage for just about every debate you’ll hear in city councils and building forums when it comes to Type 5.
The Materials and Methods Behind Wood-Frame Construction
Let’s talk nuts and bolts—or maybe logs and nails. The heart of Type 5 construction is, of course, wood. Most common is good old-fashioned dimensional lumber, the familiar 2x4s and 2x6s you see at the hardware store. These studs form exterior and load-bearing interior walls. Roofs and floors get wood joists or engineered trusses and are topped with plywood or oriented strand board (OSB) sheathing. It's rare to see pure solid wood beams these days; engineered lumber packs more strength per pound and resists warping better—key when you want straight walls and a quiet, squeak-free floor.
Sheathing holds it all together and stops the building from racking or twisting in a storm. Most homes get several layers: first the structural sheathing (plywood/OSB), then a weather barrier (think Tyvek or similar wraps), and finally siding. When you see something like vinyl, fiber cement, or wood clapboard on the outside, it's just the final decorative finish, not the stuff providing structural support. Inside, drywall is the usual finish, but behind it, insulation (fiberglass batts, cellulose, or spray foam) fills the gaps between studs for comfort and energy savings.
Construction can go up impressively fast. A skilled framing crew can raise the shell of a house in a week or less, and weatherproof it with a roof just as quick. Pre-cut or pre-fabricated wall panels shave off even more time; some developments have homes popping up, roofed and weather-tight, in a matter of days. But speed isn’t everything. Those fast timelines rely on everything running smoothly and the weather playing nice. Rain can be a nemesis for exposed wood, leading to swelling, mold, or even rot if builders don’t pay attention. Local building inspectors enforce strict moisture and termite prevention so homes last—but it’s never perfectly predictable once Mother Nature gets involved.
One other twist: a lot of newer Type 5 projects use advanced framing techniques. For example, spacing wall studs at 24 inches instead of the standard 16 saves wood and boosts insulation without sacrificing much strength. Engineered wood panels offer greater resistance to wind or seismic activity. And in larger apartments, fire barriers like sheetrock and sprinklers are often installed between units by code, making today’s wood-frame buildings surprisingly resilient compared to their 1960s cousins.
Check out the table below, which shows at a glance the key materials in Type 5 and compares them to other types:
Element | Type 5 (Wood Frame) | Type 4 (Heavy Timber) | Type 3 (Ordinary) |
---|---|---|---|
Main Structure Material | Dimensional & engineered wood | Large timber (massive beams) | Masonry (brick), steel, wood floors |
Exterior Walls | Wood or light gauge metal | Exposed heavy timber, wood | Brick/block |
Density Limit | 3-4 stories typical | Up to 6 stories (rare) | Varies, but often higher |
Fire Resistance | Poor (with fire protection options) | Better (large beams char vs burn quickly) | Good (exterior masonry resists fire) |
Construction Speed | Very fast | Moderate | Slower |
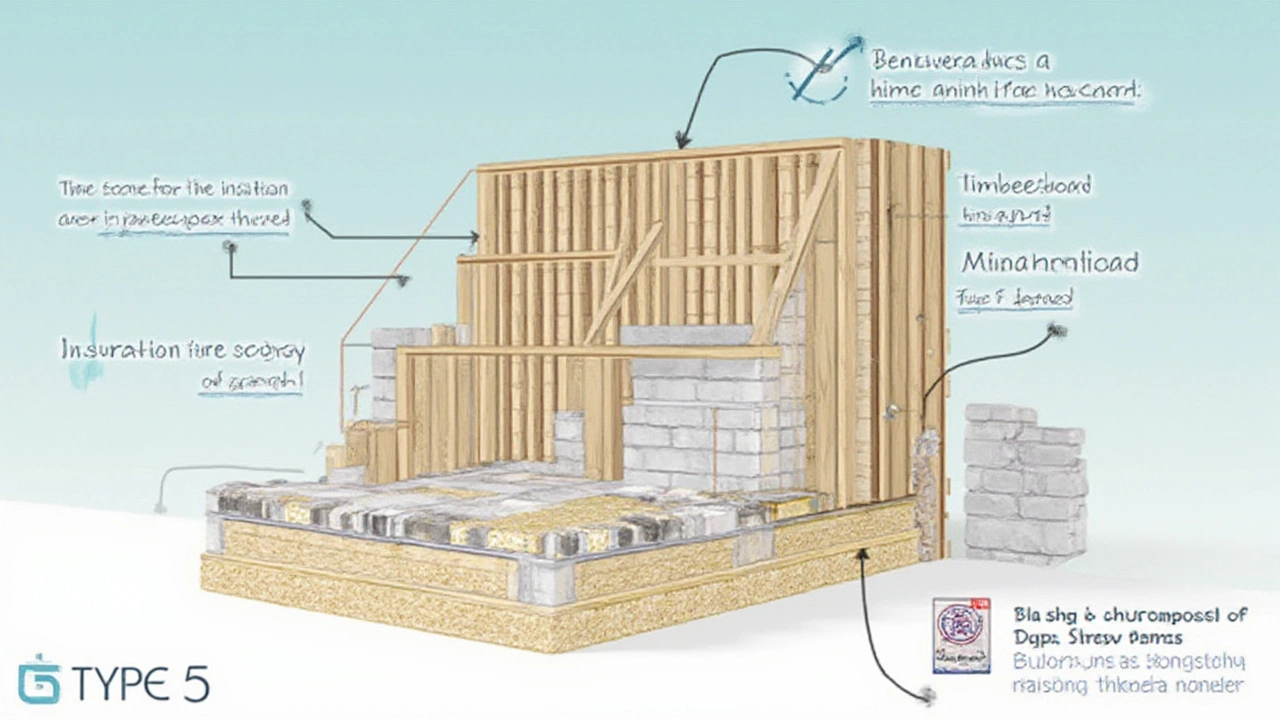
Fire Safety, Code Requirements, and Modern Risks
Fire is the big elephant in the room any time Type 5 construction comes up. There’s no sugarcoating it: wood burns, and it burns fast. When you see frightening news stories about apartments or homes engulfed in minutes, they’re often wood-framed buildings, and sometimes still under construction—meaning no drywall or sprinklers installed yet to slow down a blaze. Buildings under construction can go up almost instantly if a spark finds exposed framing, and fire crews fight an uphill battle when there’s nothing except wood to stop the spread.
Not all wood is created equal, though. Engineered wood products (like I-joists or laminated beams) can lose their strength and collapse faster in a fire than solid sawn lumber. A study in 2014 by the National Institute of Standards and Technology (NIST) found engineered wood floors failed in as little as 6 minutes after ignition, compared to about 18 minutes for solid wood—long enough for firefighters to get trapped if they don’t recognize the risk. Modern building codes have responded by requiring more layers of drywall, faster fire alarm systems, and, for multi-unit buildings, mandatory sprinklers. In fact, the National Fire Protection Association (NFPA) reported in 2019 that sprinklers reduce civilian death rates by 81% in buildings where they functioned as designed.
Code requirements keep ramping up. Most jurisdictions only allow Type 5 for residential buildings up to four stories, or for commercial spaces with tight fire separations. For multi-family apartments, fire-resistant corridors and stairwells, closely monitored smoke alarms, and compartmentalized construction are the name of the game. Clever builders seal off wall cavities to keep flames or smoke from sneaking between floors. These details may be invisible, but they’re what let folks sleep a little easier at night. And for those in older homes, retrofitting smoke detectors and fire doors goes a long way—if you live in a classic wood-frame house, that’s worth considering.
Insurance tells the same story. Many carriers offer lower premiums on homes with updated fire protection: modern alarms, hardwired detectors, and sprinklers. A less obvious factor? Your home’s distance from a fire hydrant and station can multiply your insurance costs if you live in a wood-frame house, making urban neighborhoods a bit cheaper to insure than rural ones. It all comes back to response time: the less time a fire has to grow, the better your odds.
If you own, rent, or build Type 5 homes, make sure you understand not just the risks but your local code’s specific rules. Some towns ban wood-frame apartments altogether, while others require extra-thick walls or advanced alarms. Keep an eye on building permit delays—often, it’s fire safety reviews, not structure, that hold things up on the city’s end.
The question gets raised: should we just stop building with wood completely? Most fire safety experts don’t think so. Instead, they focus on boosting the passive and active fire protections that limit disasters, like compartmentalizing rooms, using intumescent paints, and upgrading evacuations plans. It’s a balance, and it’s why new Type 5 construction keeps coming—this approach offers enough safety for modern risk tolerance, so long as the details are followed to the letter.
Tips for Owners and Builders: Getting the Most from Type 5 Construction
Living in, or building, a Type 5 structure? There are smart moves you can make to stretch the advantages while cutting down the risks. Don’t assume your home is safe just because it’s up to code—there’s more to safety and performance than the bare minimum. Here’s what really pays off:
- Type 5 construction always benefits from impactful extras like interconnected smoke alarms, not just the battery ones.
- If you’re building, insist on Class A roof coverings and exterior fire-rated sheathing. Both slow down flames in case wildfires are a threat—saving lives and your investment.
- Consider sprinkler systems, even if you’re just building a single-family home. They cost less than many realize—about $1.35 per square foot, according to U.S. Fire Administration data—and they can mean the difference between a contained fire and a total loss.
- Keep up on caulking and sealing: little gaps in wood buildings attract pests and leak energy. Spray foam or caulk in unfinished basements or attics pays off double in energy savings and durability.
- If you’re prone to storms or hurricanes, talk to your contractor about hurricane clips and extra bracing. Type 5 wooden frames flex more than concrete or steel, but extra fasteners can keep the roof from peeling off or the whole house racking in high winds.
- Monthly smoke detector checks sound simple, but always trip up even diligent homeowners. Set a recurring reminder on your phone—failures happen more from dead batteries than broken sensors.
- Want to save on heating and cooling? Type 5 lets you super-size insulation cheaply. Fill wall cavities completely, insulate rim joists where the framing meets foundations, and look at spray foam over traditional batts in crawl spaces for an energy-efficiency bump.
- Pest control matters: Carpenter ants, termites, and rodents see wood buildings as a five-star hotel. Inspections and time-tested treatments save a ton in potential damage down the line.
- Finally, if you’re renovating, double-check load-bearing status before you grab the sledgehammer. Wood frame homes are more forgiving, but every stud you pull needs to be replaced or reinforced—your house isn’t Tetris.
There are unexpected perks, too. Wood breathes, balancing indoor moisture and temperature. That “cozy” feeling in older houses comes from the way wood naturally modulates humidity and absorbs sounds, which concrete can’t fake. Restoration is easier—dents, holes, or warped trim are just a trip to the hardware store away from being fixed.
Remember: new wood-framed homes and condos outnumber all other residential construction types in the U.S. Put simply: your odds of living or working in a Type 5 wood-frame building are very good, especially in the suburbs or small cities.
Next time you step into a new house or apartment, take a closer look at those baseboards or the hollow sound behind the drywall. That’s all Type 5 engineering, quietly holding up everyday life.