Trying to stretch every dollar on a new build? You’re not alone—it’s wild how fast costs creep up when you start looking at options. If you want a cheap building method that actually delivers, it’s key to look beyond fancy ads or what your neighbor swears by. The most affordable approach really boils down to how you combine materials, labor, and design decisions.
There’s no one-size-fits-all answer, but some methods consistently land at the bottom of the price list. For example, pole barns—a.k.a. post-frame construction—can often shave thousands off your budget compared to brick or traditional frame builds. Prefab panels go up even faster and with fewer hands, and poured concrete is surprisingly wallet-friendly in the right climates.
The real secret? Cheap building isn’t just about what you use—it's also about how you plan. Picking standard sizes, keeping things simple, and avoiding unnecessary frills can save more than you’d think. Next up, we’ll break down exactly what makes some methods cheaper than others, so you can make the smartest call for your situation.
- What Makes a Building Method 'Cheap'?
- Top Low-Cost Construction Methods Compared
- Material Choices That Save Money
- Smart Design Tweaks for Budget Builds
- Pitfalls to Avoid When Building on the Cheap
What Makes a Building Method 'Cheap'?
So, what really makes one construction method cheaper than another? It usually comes down to three things: labor, materials, and how complex the build actually is. Most of your costs, whether you’re building a shed or a full-on house, come from these areas. If you can save money on all three, you’re probably looking at the cheapest building method available.
Let’s break it down a bit. Labor is a major chunk—hiring skilled workers isn’t cheap. Methods that go up fast with less specialized labor (like prefab panels or post-frame builds) will almost always be cheaper. Materials matter too. If you stick with locally available stuff or use recycled or repurposed materials, costs drop fast. Complex designs eat money because custom work takes more time and effort. Think simple layouts, straight lines, and standard sizes if you want to keep more cash in your pocket.
- Labor: Fast, simple builds use fewer workers and less time, which cuts costs.
- Materials: Cheaper options are usually things you can buy in bulk, use off-the-shelf, or get second-hand.
- Design: Fancy shapes and loads of corners mean more time (and money) to build. Streamlined, basic shapes cost less.
Another factor is local climate and building codes. In some places, a certain method is “cheap” just because it fits the rules without extra steps or paperwork. For example, in warm states, slab-on-grade concrete floors are dirt cheap. In colder areas, not so much—you might need an insulated foundation which adds to costs. Always weigh what’s cheap on paper versus what actually works (and passes inspection) where you live.
Bottom line: The cheapest methods cut out extra steps, use easy-to-find materials, and keep design decisions practical. Handy builders save even more by doing work themselves, but just be honest with your skills—nobody saves money fixing avoidable mistakes.
Top Low-Cost Construction Methods Compared
If you’re hunting for the cheapest building method, it pays to compare real options side by side. Some methods float around the web that sound affordable, but don’t really stand up when you add everything up. Here are the most common cheap building approaches actually used today, with their main perks and hang-ups.
- Pole Barns (Post-Frame): These go up fast and don’t need a concrete foundation for basic storage or barns—even some homes. Posts are sunk deep, then walls and roof get attached. Labor costs drop since there’s less to build. You trade off a bit on insulation and finish detail, but for garages, workshops, or simple homes, pole barns can start at around $30–$50 per square foot.
- Prefab Panels and Modular Housing: With prefab, most parts get built in a factory and delivered to your site. The pieces fit together like big LEGO blocks. This cuts labor time by half, according to a 2023 study from NAHB. Less time means less money spent on workers. You’re getting walls, windows, and sometimes even finishes included in the price—some modules hit as low as $80 per square foot, but shipping and crane costs can nudge it higher.
- Poured Concrete (ICF and Insulated Forms): Pouring concrete into reusable forms, especially insulated ones, makes walls that are strong and energy-smart. Up front, costs are similar to stick builds (around $100–$125 per square foot), but you save later on heating and cooling. It’s quickest in warm areas where frost isn’t a worry.
- Traditional Stick-Framing: Still the basic option for single-family homes, wood frame with plywood sheathing is easy to tweak and works almost anywhere. Material costs can swing with lumber prices, but it’s hard to beat on flexibility if you’re handy and plan to DIY some work.
Extra cheap options like earthbags or straw bale sound cool, but local code approval can cause headaches. Most folks lean toward prefab, pole barns, or traditional framing for a reason—there’s support, solid resale value, and fewer surprises with inspectors.
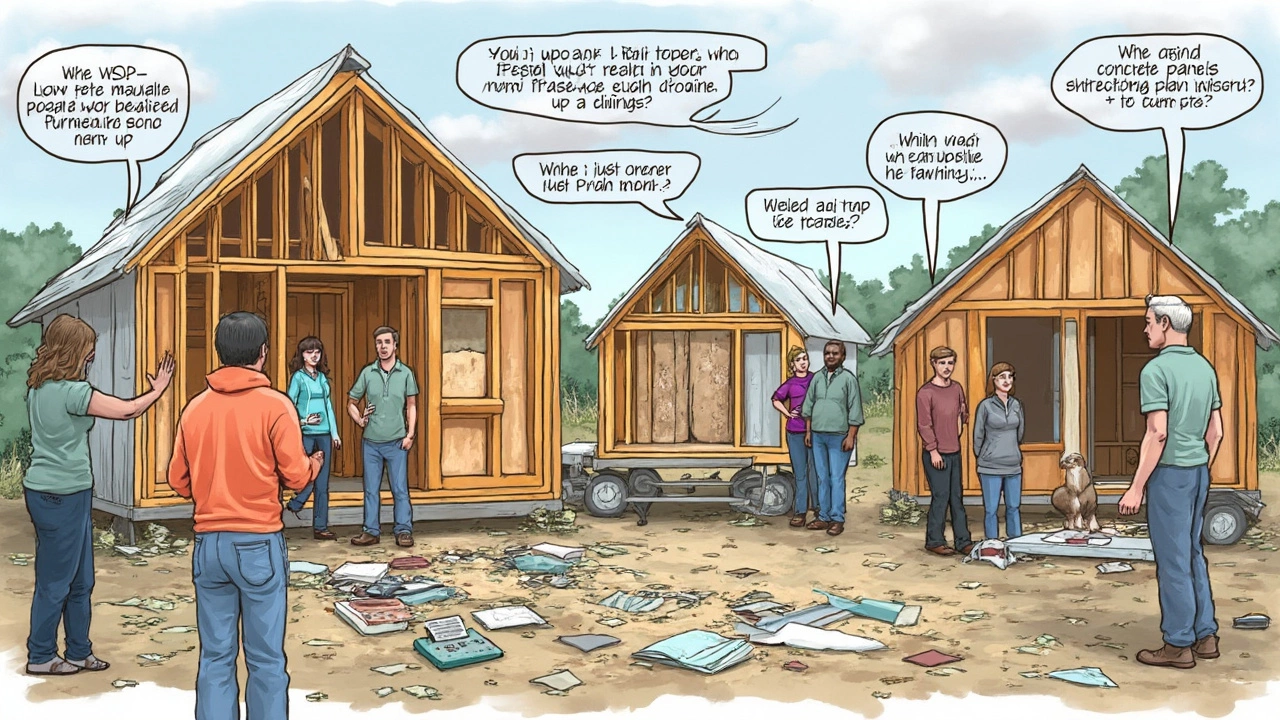
Material Choices That Save Money
Choosing the right materials is where you can see real savings in home building. Everyone wants a place that’s solid and looks good, but let’s face it—prices for lumber, brick, and everything else keep bouncing around. So, where do you cut costs without cutting corners?
First off, engineered lumber like LVL (laminated veneer lumber) or OSB (oriented strand board) is cheaper than traditional hardwoods and even regular lumber, especially when you’re framing. OSB can cost 30% less than plywood for sheathing, and these savings add up fast on larger builds.
Then there’s concrete. Using poured concrete or even concrete blocks for walls can slice costs, especially if you keep the design rectangular and simple. A 2023 market survey showed poured concrete walls can be up to 20% less expensive than brick in most states. Concrete lasts nearly forever and doesn’t need much maintenance.
For insulation, skip the expensive spray foam in favor of batt or blown-in fiberglass. Blown-in fiberglass gives good thermal performance at about half the price of spray foam. Plus, it’s easy to install, so labor runs cheaper.
- cheapest building method almost always means standard, widely-used materials like OSB, fiber-cement siding, and metal roofing. Prefab roof trusses, instead of stick-framing rafters, also cost less and arrive ready to install.
- Reclaimed or recycled materials—brick, lumber, or metal—can seriously drop your costs. Just check for quality and local codes before using anything secondhand.
- Vinyl flooring looks like wood but costs a fraction of the price. It’s popular for tough, budget builds because it handles wear like a champ.
To give you a clear snapshot, here’s a quick cost comparison table for popular building materials per square foot as of early 2025:
Material | Avg. Cost (USD/Sq Ft) |
---|---|
OSB Sheathing | $1.65 |
Plywood Sheathing | $2.25 |
Brick (wall) | $10 - $15 |
Poured Concrete Wall | $8 - $12 |
Fiberglass Insulation | $0.60 |
Spray Foam Insulation | $1.25 |
Metal Roofing | $5.00 |
Asphalt Roofing | $2.00 |
Vinyl Flooring | $2.50 |
Hardwood Flooring | $7.00 |
Bottom line—skip the fancy upgrades and pick standard materials. Stick to sizes and types that your suppliers keep in stock and you’ll avoid delays and painful price hikes.
Smart Design Tweaks for Budget Builds
If you want to keep costs low, your design choices are where you can make the biggest difference. You don’t have to settle for a boring look, but some tweaks will give you way more house for your money. For starters, keep the shape simple—rectangles and squares are your friends here. Every corner or angle adds to labor time and materials, which really stacks up fast.
Keep the floor plan compact and open. Cutting back on hallways and sticking to fewer interior walls saves on framing, drywall, and even HVAC needs. Open layouts aren’t just trendy—they’re wallet-friendly. Avoid high ceilings if you’re serious about savings. Standard 8-foot ceilings cost less to build and heat than vaulted or two-story spaces.
- Cheapest building method tip: Use stock plans instead of custom architecture. Ready-made plans are widely available and much cheaper than starting from scratch with an architect. You can find some online for under $1,000.
- Bundle your plumbing. That means keeping your kitchen, bathrooms, and laundry close together—less pipe, less labor, less cash out the door. Same idea goes for electrical runs.
- Standardize window and door sizes. Special order units eat up your budget fast. Stick to what’s on the shelf at your local store, and you’ll save both time and money.
- Finish the essentials, and leave some space unfinished. Lots of people finish basements or garages later when the budget allows.
- Ask your builder about value engineering. This means tweaking the design to cut out anything that’s unnecessarily complicated or pricey, without ruining function or durability.
Most important: stick to the plan once you start. Constant changes during the build are where most budgets go sideways. Basically, simple wins. Use what’s standard, keep spaces open, and don’t get caught up in extras you don’t really need.
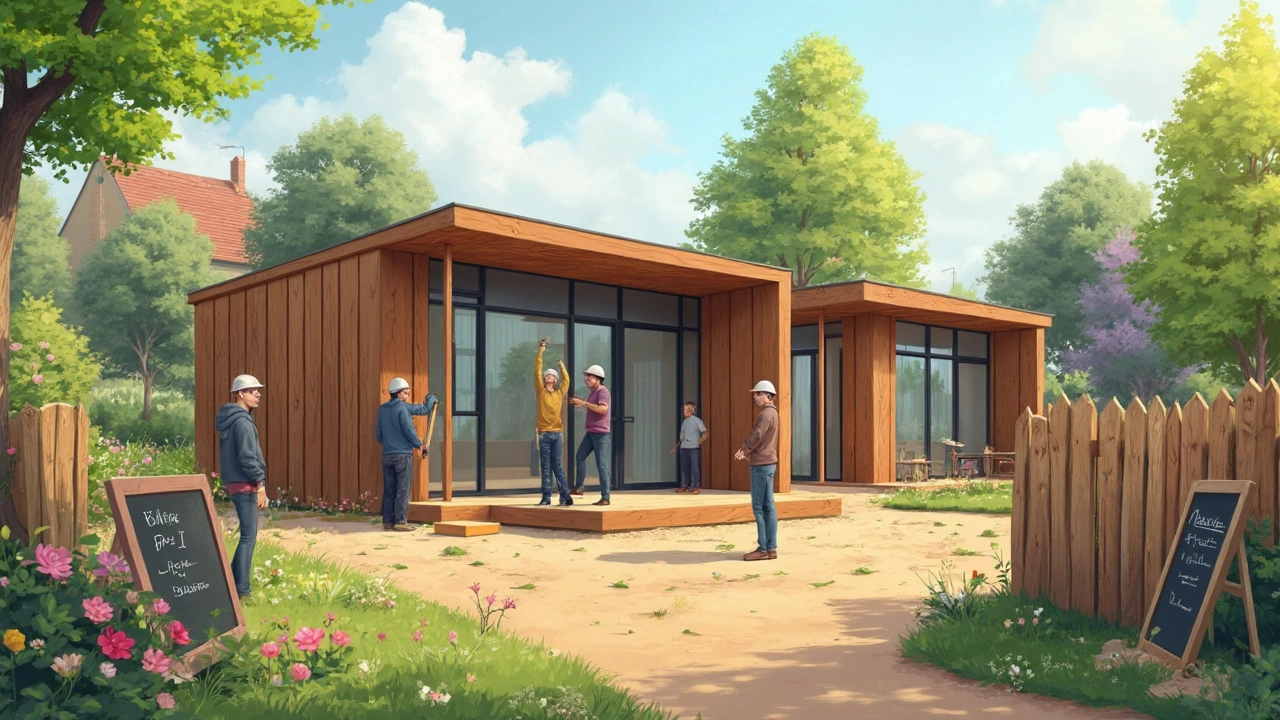
Pitfalls to Avoid When Building on the Cheap
Saving money is awesome, but cutting too many corners can land you with headaches, wasted cash, or a home you regret. There are some common traps people walk right into when they chase the absolute rock-bottom price.
- Skipping permits and proper inspections: Don’t get tempted to work without all the right paperwork. Local building codes exist for a reason, and if you ignore them, you can face fines, delays, or even have to rip out finished work. It’s happened time and again—someone brags about saving a few grand, only to lose double fixing mistakes down the road.
- Going too cheap on key materials: Opting for bargain-basement windows, doors, or roofing might feel smart up front, but these are the areas where poor quality bites back. Cheap windows leak, junk roofing needs repairs early, and flimsy doors won’t last a few seasons.
- Hiring the lowest bid without checking references: It’s easy to pick the cheapest contractor, but sometimes ‘cheap’ means unfinished work, weak warranties, or flat-out shoddy results. Always read reviews, check their previous jobs, and get everything in writing.
- Bad planning with design and site prep: Trying to improvise or skip a solid plan leads to wasted time and surprise costs. Measure twice, plan properly, and account for site conditions—bad drainage, unstable soil, or access issues can all turn a ‘cheap’ build into a money pit.
- No contingency in the budget: No matter the method, don’t blow your entire stack up front. Have a buffer—usually 10-15%—because nearly every new build throws at least one curveball your way. Things like unexpected weather, price hikes, or delayed deliveries are almost a guarantee in construction.
Penny-pinching is fine, but you still want a place that’s safe, sturdy, and lasts. The cheapest building method can save you real money, but cutting the wrong things often means you’ll pay more to fix it all later. A little extra upfront can save a fortune—you don’t want to learn that the hard way.